Pouring a Micro Keel
by peter lenihan ellengaest@boatbuilding.com
I poured my Micro keel in the winter of '93 and I
used a number of references before handling all that hot lead! Namely, ''Bud''
MacIntosh's How To Build A Wooden boat. Here I learned that you need a good constant
source of heat. I rented one of those propane burners used at corn roasts etc. and
had plenty of heat for the duration of the melt down and pour. Next came a discarded
hot water tank which I then had cut open on the side and had legs welded on to it so that
it would lay horizontal and high enough to get the burner underneath. A length of pipe was
then fitted with an elbow and screwed into the ''lower'' drain tap of the tank. It
was snugged up just enough so that I could pivot it 90 degrees, that is, from a position
at right angles to the tank to one running in line with the tank. The mold is then
positioned such that when you do lower the pipe,the open end rests on the edge of your
mold. The mold was simply a long rectangular box with the boat's bottom profile and the
bottom of the keel defined by a tight/close fitting silhouette made up from 2X2 clear
pine. Before sandwiching the whole works together with 3/4 inch plywood, both halves
were liberally coated with waterglass (sodium silicate,available at most good hardware
stores,at least up here in Montreal). |
|
I have spent the last 6 years
sailing my Micro on the St Lawrence River around Montreal and despite dealing with a
minimum 1.5 kt current (much faster as you get closer to the Lachine Rapids!), absolute
mayhem from the wake of hundreds of speed boats and staying out of the way of ships going
through the St. Lawrence Seaway, my Micro has never, read never, let me down in the
sailing dept.! She routinely out sails a couple of Matilda 20's from my club and regularly
sails |
right past the fleet of 404 sloops from the local sailing
school! Of course, in super light air no faster than the current, one does become
rather proficient in moving backward while trying to maintain the illusion of forward
motion.......enough to make you sick if you sight a spot on land and watch it move ahead
while the boat is moving forward through the water but backward over the bottom.
My sails were ordered through Common Sense Designs in
1993. The main has lots of camber in it while the mizzen appears to have just a
hint. Taking up on the mainsail snotter will do wonders for boat performance; let it
out a bit in lighter winds and get it in tight when the wind picks up until reef time. |
Here are some pictures of
my keel pouring adventure for my MICRO
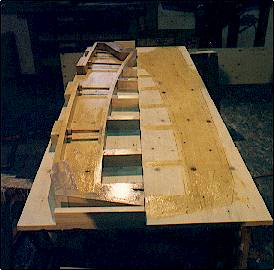 |
1) The two halves of the mold just prior to
assembly. The insides have been coated with "water glass" (sodium silicate). The
framing for the mold is from 2x2 pine. The wooden dowels indicate where the future keel
bolts will pass through the keel. |
2) One half of the mold in the upright position.
Notice the gap in the 2x2 framing, this is where the molten lead will enter once the mold
is assembled and placed "upside down." |
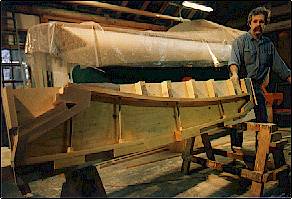 |
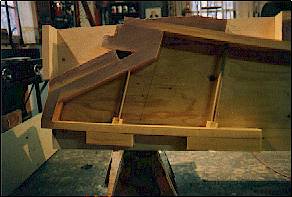 |
3) Close up of keel bolt dowels showing also the
"wooden nuts." This will allow me to tighten up the keel bolts from within the
boat and leave the outside bottom of the keel smooth and fair. |
4) The Big Day! Here we can see the
"recycled" hot water tank, propane burner, mold and fire extinguisher ready to
begin. |
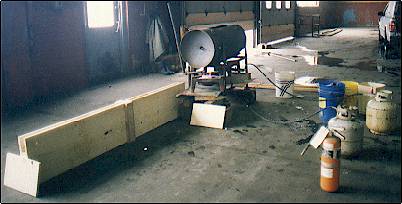 |
5) Just before pouring
the molten lead, a small propane torch is used to heat up the spout so that the lead will
not congeal inside the spout/pipe. |
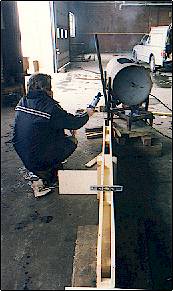 |
Note the blocking for the mold and level to ensure
that all is set and true. By the way, this operation is best done outdoors. We did it
inside, with a door left open. It was a cool 18 degrees outside. 6) Once all the lead had been poured and while it was still liquid, we
used a steel rod to agitate the lead to release any trapped air bubbles. |
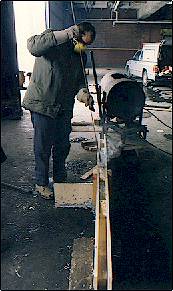 |
Note the lead
splatter on the floor? Wear protective clothing and mask! |
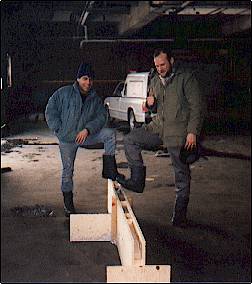 |
7) Back from lunch one hour later. The keel is
still rather hot but the lead is congealed. My two happy helpers are relieved! |
8) Oh! Oh! The moment of truth! Unscrewing one half
of the mold to check out the keel. |
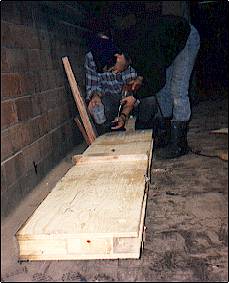
|
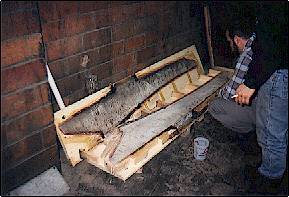 |
9) Success! No voids or anything else strange other
than some really charred wood. This shot was taken approximately 2 hours after the pour,
and the lead is still too hot to lay your hands on for very long! |
10) The mold has been re-assembled with clamps to
stand the keel upright and to clean out the holes for the keel bolts. Notice the nice
clean recess for the nut at the bottom of the keel. |
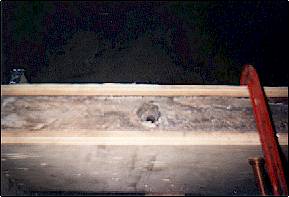
|
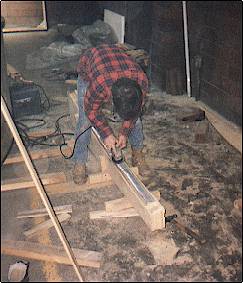 |
11) Prior to "offering up" the keel to
the hull, we used a 4" right angle grinder to dish out the mating surface of the keel
thereby allowing for a nice pocket of Sika Flex to form a gasket around the keel bolts. Up
until actual attachment to the hull, the lead was kept in the mold to prevent it from
bending out of line. It is remarkably prone to this, if you do not brace it. |
12) Skids were placed under the boat and the keel
nudged along sideways until in position under the hull. At this point, the fore and aft
dead wood are already in place. |
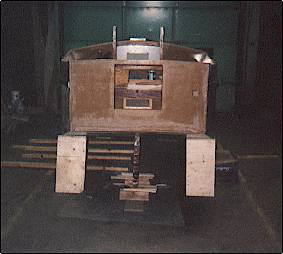
|
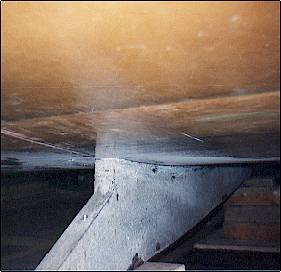 |
13) Aft end of keel after being raised up to the
hull with a small hydraulic jack and blocked. |
14) Forward end of keel. Note nice clean fit with
bottom of the hull. |
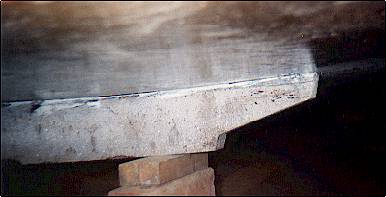 |
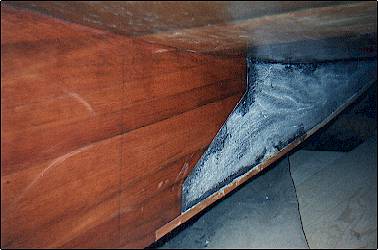 |
15) Aft end of keel, keyed into the deadwood, keel
shown in place and lead cleaned up with grinder. |
16) Same shot, showing forward end of keel. |
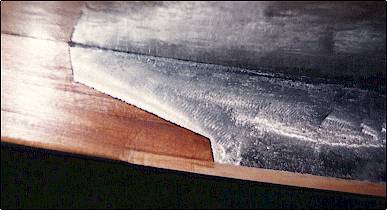
|
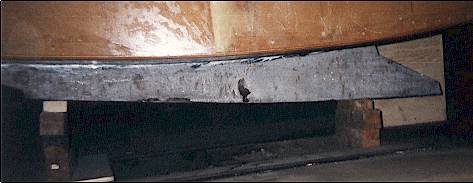
|
17) The keel in place without deadwood. Its
location was established by consulting the plans. |
18) Forward end of keel just before application of
barrier coat. |
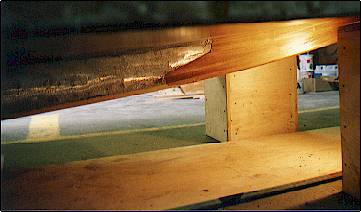
|
19) Aft deadwood, comprised of 2x2 mahogany
laminate awaiting installation of "stern post." |
20) "Stern post" in place with 12"
drift bolts going into deadwood. |
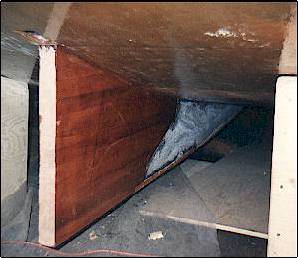 |
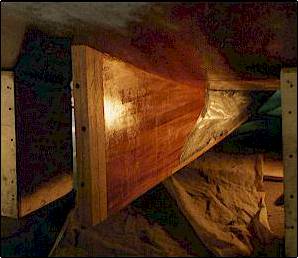 |
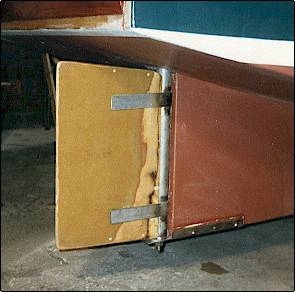 |
21) Keel job completed and now "fussing"
with the rudder... |
22) The boat hauled outside just to see if the mast
really does fit! |
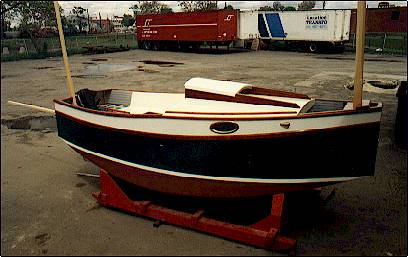 |
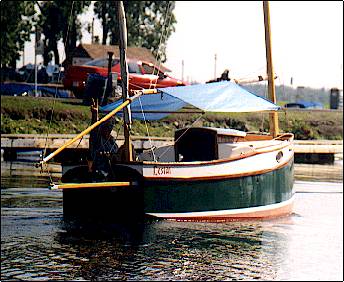 |
23) Hot, muggy and no wind? No problem! Just set up
a simple awning, put the motor on slow, fill up the cooler and go! |
24) On the other hand, give me a bit of wind and I
am gone! |
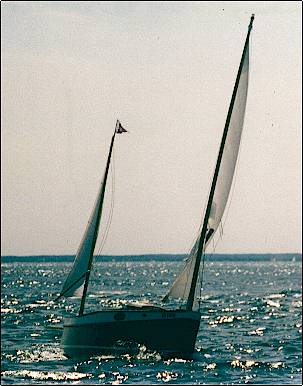
|

|