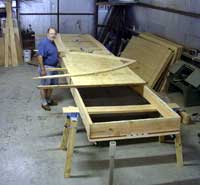 |
Here is the strongback that the boat is built
on. Later Jim put casters on the bottom and lowered it to
the floor. Those curved things are the 'shelves' which will
later attach to, and define the shape of, the sides of the
boat. |
|
While the strongback was still on the sawhorses, Jim used
it for a workbench and built a number of components including
the transom. |
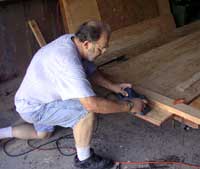 |
The boat will be some 25 feet long so the bottom and side
pieces were scarphed together at this time. Jim used a Bosch
electric hand planer to taper the edges of the ply. |
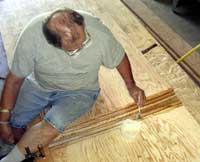 |
Both sides of the joint are epoxied until they will not
take any more (to avoid a glue-starved joint) then joined. |
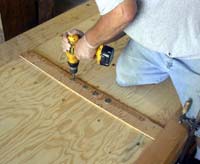 |
Jim used screws and fender washers, per the book, to hold
the joint together until the epoxy set. |
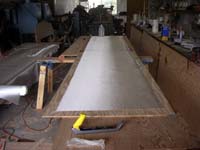 |
After the side pieces were scarphed together, one surface
was glassed. |
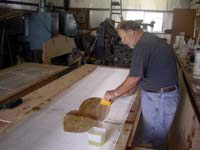 |
Jim used a squeegee to spread the resin - the cloth was
rolled out onto dry plywood. This method did not follow
the book, but it worked well. |
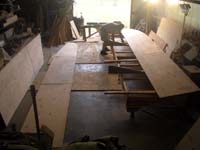 |
In this picture you can see that Jim has built two V-shaped
supports and clamped them to the strongback. Then he placed
the precut panels on to begin the bottom assembly. |
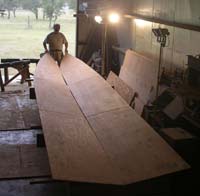 |
Both panels are now in place and Jim is testing the flexibility
of the forward sections. The rear sections of the bottom
are 1/2" thick, but the bow panels are 1/4". Later,
another 1/4" will be laminated to the bow. |
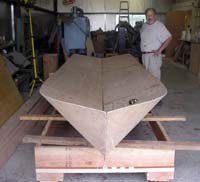 |
I helped hold the bow sections in place while Jim wired
them together. It was easy to do. |
|
Jim epoxies the forward section of the taped fillet. We
painted resin on first, then applied a wood flour and epoxy
fillet, and while that was still soft, laid two strips of
12 oz. biaxial tape. |
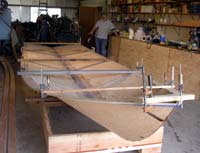 |
The last part of the bottom sub-assembly is the chine
flats. Here they are held in alignment before being epoxied
in place and taped. |
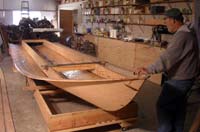 |
We also glassed the entire inside of the bottom at this
time. The next day, Jim tried out the longitudinal stringers
for fit. |
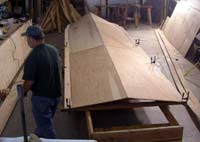 |
Then he removed the stringers and we flipped the bottom
sub-assembly so he could tape the bottom of the keel joint. |