|
The Joy of Leading
by Andrew Linn
The Cultus Hehtheht (our PDRacer) will have 2 pieces of
wood that hang down into the water: The leeboard (the big
one) and the rudder. The leeboard helps control lateral -
sideways - movement and the rudder steers the boat. Being
wood, these float, and so must be weighted to keep them in
the water. |
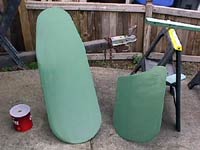 |
(click images to enlarge) |
As usual, there is math involved. According to websites,
the leaded area should be about 7% of the surface area that
will be under water. My rudder is 16x20, or 320 sq inches,
requiring a cutout of about 22.4 sq inches. I decided to go
with a 5x5 cutout for the rudder and a 4x9 cutout for the
leeboard (25 sq inches and 32sq inches). I drew the square
near the bottom of the leading edge of the rudder and drilled
through the corners of the square to make cutting easier. |
Cutting couldn't be easier. Take the jigsaw and get going. |
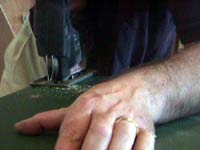 |
(click images to enlarge) |
Lead shrinks as it cools so the websites say
to bevel the edges of the cutouts to create a lip the led
can grip. I used a 45 degree router bit. I normally hate routers.
as a kid of about 6 or 7, my carpenter grandfather told me
"Boy, of all the tools in this shop, the one that'll
most likely chew you up is this here router." I am 41
years old, and am still terrified of routers. |
Finally, the websites suggest driving nails around the perimeter
of the cutout to act as anchors. It was easier to drive the
anchor nails into the 5x5 hole than the 4x9 hole, but I got
them in. |
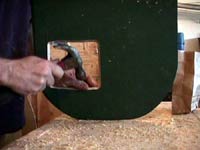 |
|
And here are the pieces, ready for leading.
7% of the wetted area, beveled edges, anchor nails around
the perimeter. |
I got this lead for free from a tire shop, the guys were
more than happy to help. Lead weighs .4lbs per cubic inch,
and my rudder / leeboard are about .4 to .5 thick, so for
the rudder, I anticipated needing between 4 and 5 lbs of lead.
I should have added some padding to this, maybe doubling the
amount just to make sure I had enough ready. |
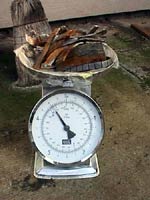 |
This is the foundry. Notice I am outside - lead fumes are
poisonous. The crucible is a coffee can with a 3/8 inch hole
drilled 3 inches up from the bottom. The heat source is propane
and the furnace is the base for my turkey fryer. I like that
as a furnace because it has a nice, wide base.
I clamped the rudder to a cookie sheet, intending for the
cookie sheet to act as a backstop. There were 2 problems with
this: 1) The clamps made for an uneven base which I did not
account for - the lead pooled in one corner. 2) The cookie
sheet was uneven - especially when heated - and the lead flowed
out through gaps. This was a failed try. I had to pound
out the lead and think about what I was going to do. |
The next day I tried again. I nailed scrap plywood
to the backside of the rudder, making sure it made a good
seal. I leveled the whole operation out with more scrap and
weighted it down. Notice that the crucible is close to the
work area - I didn't want to be hauling a bucket of molten
lead all over the place. |
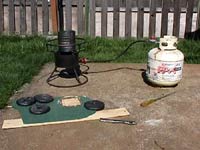 |
|
Not a good picture, but once poured, the lead
would bubble, probably from smoke or steam being released
from the plywood backstop. It didn't splatter much, but it
did splatter, so be aware and be careful. |
This is what I ended up with. Notice the scorch
marks on the backstops and the divots in the lead caused by
gas bubbles. Lead melts at something like 480 degrees and
paper burns at 451 degrees, so I suggest you pour your lead
as soon as it melts - within seconds - to prevent the lead
from heating so much the wood catches fire. |
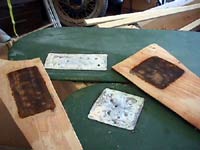 |
|
I smeared Elmer's Exterior Wood Putty into the
divots and around the edges, then sanded it off smooth with
a belt sander. This was probably the stupidest thing I did.
If lead fumes are dangerous, ground up bits of lead being
kicked off by a belt sander are probably worse. |
Here is the finished product - it isn't glass
smooth, but it isn't bad, either. If I was doing this for
a real racing boat, I would probably fiberglass it in as well. |
 |
This leading is completely doable by the backyard boat builder.
I didn't have any experience with this before I started. I
did some research on the web, asked some questions, and used
my head. Dress appropriately - all leather and natural fiber
stuff just in case there are spills, eye protection, leather
gloves and apron. Do it outside. Use your head. Be careful.
|
|
|
|