Bayside Boatshop |
|
by Ross Lillistone - Esk, Queensland - Australia
Polyurethane Glue |
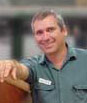 |
I've been using Purbond for three and a half years, during which time my workshop has produced around twenty-four boats ranging in size from 7ft to 24ft LOA.
When it comes to glue and paint, I'm very conservative - I can not afford to have a component fail, or my reputation (for what it is worth!) is gone and I could possibly face legal action. Therefore, I do lots of testing, and ease into the use of any product which is new to me.
With Purbond, I started out using it on non-critical items such as strongbacks and jigs. The next stage was using it as the primary adhesive in a 9 1/2ft x 4ft glued-lapstrake boat-shaped cupboard. The cupboard was built as though it was a real boat, but of course it has never seen the water. It is 40 months old and is still holding together despite constant use in the most popular restaurant in Manly.
The first "front line" application was (and still is) in the lamination of spars. These have ranged from the simplest solid masts, booms and yards made up of two, solid laminations, to eight-sided birds mouth hollow tapered masts of 18ft in length. I have a standing agreement with my customers that all components are guaranteed for life (theirs or mine) while in the hands of the original owner. So far there have been no failures. They used to glue up spars using fish glue - large gluing surface areas and loads mainly in shear.
Second on the "front line" applications for me was the use of Purbond as the inter-strip adhesive in strip planking. This is another example of conservative application of a product with which one is not familiar. In the first boat built this way, I backed up the glue with 316 grade stainless steel edge nails, and it must be remembered that the strips are reinforced by the application of correctly sized 'glass set in epoxy. After building two boats with this method of stripping, I moved to the use of tongue-and-groove strips. These were glued with Purbond, but received no edge fastenings. Once again, the application was conservative as the strips were subsequently laminated with two diagonal layers of 3mm hoop pine plywood set in epoxy, as required by the design.
I had heard that some operators were scarphing plywood sheets using purbond. This seemed to me to be a more severe application, so I did some tests. The test pieces were 6mm pacific maple marine ply with an accurately cut 8:1 scarph. Some were vacuum bagged for a really tight glue line, and some were laid up in the normal manner i.e. clamps/staples/nails. Results were fairly uniform, with the best being the vacuum bagged examples. Generally, the scarphs failed in the glue line, but with about 50% of the suface area showing wood fibre failure. When using epoxy in the same situation, I have never experienced a failure in the glue line.
My informal research continues, but my opinion so far is as follows: -
- Purbond is stronger than timbers such as Western Red Cedar;
- Purbond is about the same strength (across the grain) as Silver Quandong/Hoop Pine/Oregon;
- Purbond is weaker than dense hardwoods;
- Purbond is easy and convenient to use;
- Purbond is economical;
Adhesives need to be used in a manner which is appropriate to their characteristics;
A conservative approach should be taken when using new products;

More columns by Ross Lillistone:
|