Part One - Part Two
Finding Materials; Wood
Deciding which boat to build proved to be less difficult than the procurement of the proper materials with which to build her. In this part of the world there are hardware and lumber stores which cater to a class of builder less discriminating than most first world builders. Although lumber and plywood is readily available, good marine plywood is very expensive and less favored by those who need a cheap boat from which to fish for profit or food. What passes for marine lumber here I wouldn't use to construct an out-house.
The number and size of plywood voids (if filled with water) could float a battleship, and the thin veneer plywood surfaces would make toilet paper look like sheet-rock. Obtaining just any old lumber and plywood is not difficult in this fair land. What's hard to obtain is accurately dimensioned and sound lumber, and void-less marine plywood with surfaces thicker than paper.
You just can't walk into a home depot around here and load your shopping cart with most everything you need to construct a boat. There is no single store in Cebu with that much service, knowledge, or inventory. After several months of investigative resource hunting in my area, and after deciding to build what I thought was a well-designed and serviceable '50s or '60s style sailboat, for which, as I mentioned, the plans were free, I ordered Philippine mahogany to size from one of the larger lumber yards, and 5 sheets of export quality 4x8 Santa Clara plywood (recommended by my new friends at Pinoyboats.org).
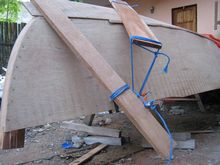 |
I ordered Philippine mahogany to size from one of the larger lumber yards, and 5 sheets of export quality 4x8 Santa Clara plywood. |
Sourcing Screws
Fasteners were the next consideration which taxed my limited American patience. The plans called for brass or stainless-steel screws in various sizes. As even the large Banka boats are mostly constructed with copper nails, finding brass screws in multiple sizes became complicated.
I don’t remember how many different locations my wife and I searched to find stores with proper fasteners, perhaps 20 or 30, but the process took way too long. Eventually, three stores were found within several miles of each other that could produce on demand one size or another. I failed completely to locate stainless lag bolts for the stem, so I instead used some creative carpentry to make the wood joint stronger.
Epoxy
By far, the easiest boat building material to find was epoxy. It can be purchased at almost any hardware store. As the shelf life codes are difficult to read one is advised to find stock which looks fresh; meaning, the container should look relatively new, not too dusty, nor show signs of corrosion. Upon request the store clerk will open the container whereby you may judge the contents for normal consistency. The savvy buyer will avoid stock which shows significant ingredient separation. Relatively inexpensive locally made epoxy, which looks and spreads like peanut butter, comes in various size cans. Two gallons of the stuff costs about 38 dollars; one gallon is part A, and the other is part B. Smaller pint and quart sizes are sold at a price proportional to their volume; there is no monetary advantage to buying larger volumes.
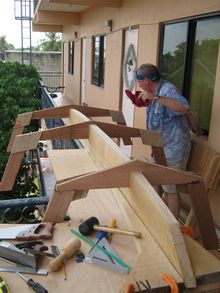 |
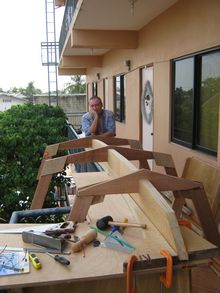 |
Philippine epoxy does not mix easily. Superior upper body musculature is required to blend part A and B together. Some aid in mixing is achieved when both cans are left in the sun for 30 minutes, and is recommended. If a runnier epoxy is desired, a small amount of thinning agent may be added after the two parts are well mixed. Adding a thinner to Philippine epoxy is sort of like trying to blend water into a can of cream of mushroom soup; the lumps will drive one crazy until a consistent mixture evolves.
After failing miserably to produce consistent epoxy batches, and after consulting with local boat builders as to how they do it, I elected to follow their example and advice, abandon the use of a mixing cup or bowl, and as unlikely as it sounds mix the epoxy parts on a flat surface with a two inch putty knife. My batches improved immediately, and I didn’t seem to have to use as much muscle. Scraps of board, or random areas of my 3/4 plywood temporary work bench, provide the perfect mixing venue. For cleanup I just spread out the remaining epoxy residue in place and let hit harden. A significant portion of my unfinished work bench is now waterproof and protected from abrasion by left over epoxy.
Fortunately, the 1:1 epoxy mixture is not all that critical and, no matter how badly one fudges the ratio, hardens well within 4 to 6 hours and is completely cured in 24. I found the "that looks about right" approach to work pretty well. The only failed joints I've experienced were my experimental short scarfs.
Epoxy is considered the number one boat construction glue in the land. Although several wood glues (dry and wet) are in good supply at most hardware stores, you will not see waterproof glues like Titebond or Gorilla glue. Epoxy seems to serve the general boat building populace well enough. Considering the rough nature of most local boat construction projects, I suppose the gap filling properties of thick Philippine epoxy comes in handy. The price is so reasonable that it's used not only for all boat joints, but as a Bondo to fill gaps, plug holes, and cover mistakes as well. It is absolutely invaluable.
Whereas thin epoxies are sometimes thickened with micro balloons, flour, or saw dust, Philippine epoxy must periodically be thinned. Many different thinners are useful. I’ve witnessed some builders using diesel fuel, gasoline, or paint thinner. I must admit to being relatively ignorant as to the effectiveness of these, for I have only experimented with what I believe to be a safer alternative; denatured alcohol. I read somewhere on the internet that denatured alcohol was a useful epoxy thinner, so, I tried it and never looked back.
I have experimented some with alcohol thinned epoxy on critical joints like chine scarfs. Sometimes I not only thin the epoxy, but I brush the joint with straight alcohol before applying the epoxy. I'm in hopes that the alcohol further thins the epoxy enough to draw it into the wood fibers to add strength. Every scarf joint I’ve made using this technique has lasted, whereas some of the other joints have failed.
This experimentation is not conclusive so don’t take it as the last word in joint work. Have some fun on your own to see if the technique works for you. Perhaps the normally thinned epoxies available in your country wouldn't need this type of preparation, although, it is something to think about.
Hand Tools
Other than the use of a power drill and a recently acquired 3 inch grinder, my boat has been fashioned with hand tools. And, whereas when I started this project my good wife had some concerns about the health of my aging body, she and others have recently commented that I no longer look like an old man. Apparently, as a side benefit to using hand tools, I’ve gained upper body strength and overall stamina. I’m not yet looking like Hercules or Clark Kent, but feeling is every bit as important as being, and I feel a bit younger than my 53 years.
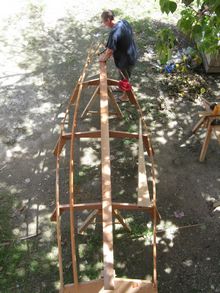 |
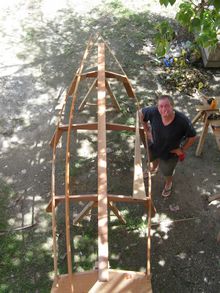 |
Because of this project I now know more about hand saws than I ever intended to. Before building this boat I would have estimated my lifetime hand saw experience to be less than two hours. I increased that by a factor of 4 within the first few days. Sawing the 2 inch thick 12 foot strong-back took 12 hours alone. Add to that the time to saw gunnels, chines, stem, transom, frames, 3/4 and 3/8 plywood, keel, skeg, and other related pieces, like saw horses, and one sees the accumulation of several normal lifespans worth of hand sawing experience.
I now own more hand saws of various design than all the saws I have ever owned put together; each one, I found, has a different job. The most interesting is the Japanese pull saw. I love to use it and go out of my way to find uses for it. My second favorite is the 22 inch Bahco that cuts through lumber like butter; unfortunately, I did not yet possess it when I labored to cut the strong-back.
In the beginning, planers were just as foreign, but now I feel like a planner expert. All phases of construction have improved my awareness of tools. I now clamp with the best of them, and use a spoke shave like a razor. Chisels are as familiar as a ball pen, and I can cut scarfs with a pocket knife (Not really). Up until I started this project I never even touched a wood rasp. I now find its employment so useful that I’ve acquired a rather costly one. So expensive in fact that my wife still looks at me crossed eyed when she sees it in my hand. All of these hand tools have brought my arms and torso back into shape. I’ve been challenged recently to arm wrestling contests by the young pups around here; I rarely loose.
Power Tools Wish List
Power tools are in many ways a blessing. For repetitive jobs, like pre-drilling and screw fastening that may otherwise cause harm to existing cartilage, I’ve required the use of a corded drill. I own and sometimes use a set of screw hole hand cores for odd jobs, but when a vast number of screws are required to fasten plywood panels to the boat sides I pull from the tool box my premature arthritis prevention; the electric drill.
I have not yet found much use for the grinder, even with the high speed sanding disk installed. But when I did need it I was glad to have it. It came in handy when finishing the inside radius of the curved stem.
I’ve given some thought as to what other power tools I might eventually buy. At the top of the list is a good sander. I’m sure it would come in handy during the finishing phase. I’m also attracted to reciprocating saws. They don’t seem to be very popular in this country, but I’ve already envisioned several applications. Cutting the plywood overhang at the chines is one. Carving out plywood panels is another. Of course, a circular saw might do as well, but the reciprocating saw is fun to use, and as I see it, much handier.
By contrast, electric planers are very popular here. I certainly could have used one for all the jobs for which I used the hand planner, like, fairing the frame, which was extremely exhausting. The disadvantage of electric planners are their noise signature which resembles that of an aircraft carrier flight deck during flight operations. All in all, I've done well with the tools I own. I’m sure my neighbors appreciate the practice of hand tool noise abatement.
Afterthought and Conclusion
The Philippine sun is unrelenting from early morning to very late afternoon. As you may judge from the photos the boat is being built outdoors with only some tree shade at certain times of day. While boat building I may consume a bathtub of water to prevent dehydration. At the end of a work day I feel like every sweat gland has been pumped dry. The real drawback to working hard in this kind of humidity is that clothing becomes extremely uncomfortable when saturated with moisture and grime. There's not much I can do about that except to take in more liquids and enjoy a refreshing cool shower at intervals. A shower every few hours does much to improve my disposition, odor, and fun factor.
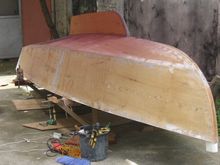 |
As you will note from the lack of finished boat photos my boat is not complete. |
As you will note from the lack of finished boat photos my boat is not complete. I have, at the time of this writing, begun to install the bottom panels. After the seams are taped and epoxied I will turn the boat over to fit the seats, trunk, mast, and rudder. Although it's been a journey worth taking I don’t know if I'd have the energy to do it again. I suppose having access to a garage or storage building might have made the process more enjoyable, but hauling tools and materials three floors every day, as weather permits, gets a bit old.
I'm constantly reminded that to avoid headaches and frustration with a project this size, it's beneficial to plan ahead. Perhaps finding materials in first world nations is less time consuming, but here, as in other developing nations where the distribution of goods and services is at a minimum, boat building can be a tremendous challenge.
Plans
|